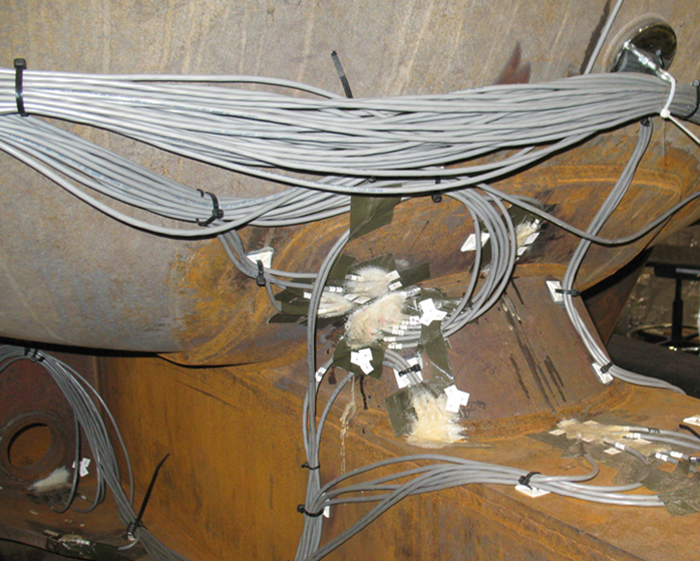
Designing and conducting physical testing of structures
We have performed numerous full-scale static and dynamic tests on various structures and are experts in the application of measurement equipment including strain gages, load cells, signal amplifiers, accelerometers, etc. With the aid of finite element analysis software, HLA can optimize the test design; provide correlation analysis for test data and provide FEA simulation.
HLA has:
Reaction Frame Structure
Designed a reaction frame structure to test ISO tank containers per “Rules for Certification of Cargo Containers.” Some of the required tests included 9 high stacking, lifting, transverse racking, longitudinal racking, etc.
Proof Test
Performed a proof test to establish the maximum allowable working pressure (MAWP) for an obround nozzle in a cylindrical vessel per ASME Section VIII, Division 1, UG-101. The strain measurement test procedure per UG-101(n) was used for this test.
Test Plan
Reviewed and rewrote a test plan and redesigned equipment set-up for the physical test evaluation of a DOT 312 cargo tank, rail-type rollover guard. Our experts supervised the test and provided on-site guidance, as well as an independent report of the test events and results.
Testing Intermodal Shipping Containers
Performed many physical tests on intermodal shipping containers to verify the buckling capacity of corner posts. Our engineers redesigned the test frame to allow compressive tests in excess of 250,000 pounds, instrumented corner posts with strain gages to indicate the onset of buckling, designed and wrote the test plan, supervised testing and collection of data, reduced data and provided a final report.
Load Cell and PC-Based Data Acquisition
Designed a load cell and pc-based data acquisition system to study the cause of the side panel buckling of a foldable airport boarding tunnel. The real time wheel loads over the side panels were sampled and analyzed when the tunnel was under various operating conditions.
Advanced Software and years of experience
HLA utilizes advanced software such as Autodesk Inventor, Pro Engineer and SolidWorks in our design efforts. Our in-house engineers possess years of experience in designing and drafting pressure vessels, piping, industrial structures for power generation units, ISO tank containers, cargo trailers, railcars and more. We can create engineering drawings and detailed fabrication drawings per your requirements and our design department can act as an extension of your in-house drafting department. Solid modeling can be utilized to model difficult 3D parts and then be used for FEA meshing to create the necessary details for a fabrication drawing.
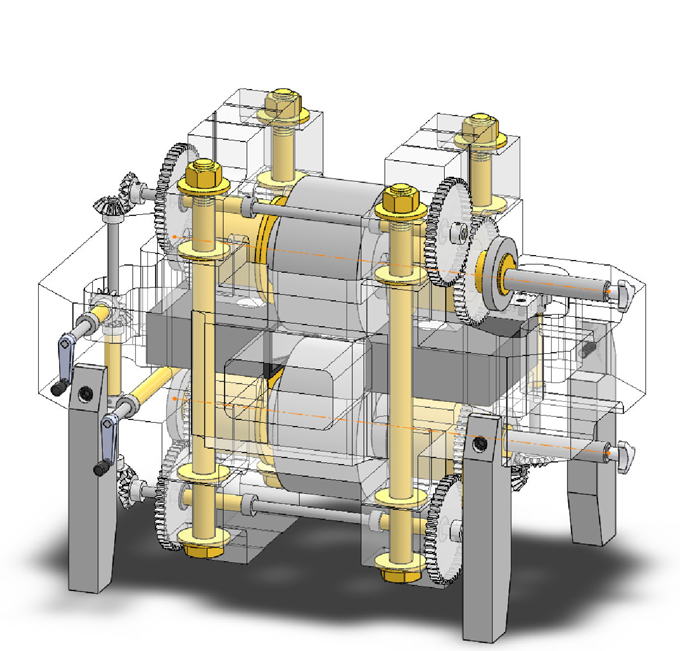
HLA provides the following:
Mean Stress Effects
GOODMAN & HAIGH Diagrams, Design Charts
Low-cycle Fatigue
Neuber Notch Strain Analysis and Strain Life Analysis
Damage Accumulation
Linear And Non-Linear, Miner Rule
IIW Nominal, Structural Stress Effective Notch Stress Fatigue Assessment
Load Spectrum Development
Sequence Effects, Truncation, Clipping, Retardation
Vibration and Spectral Density Analysis
Modal, Harmonic PSD random and Seismic vibration
Crack Initiation
S-N Curves, Endurance Limit and Fatigue Strength Surface & Size effects
Stress Concentration
Data Load Streamlines Analogy
Damage Tolerance
Software
We have several in-house and commercial software for Fatigue Analysis
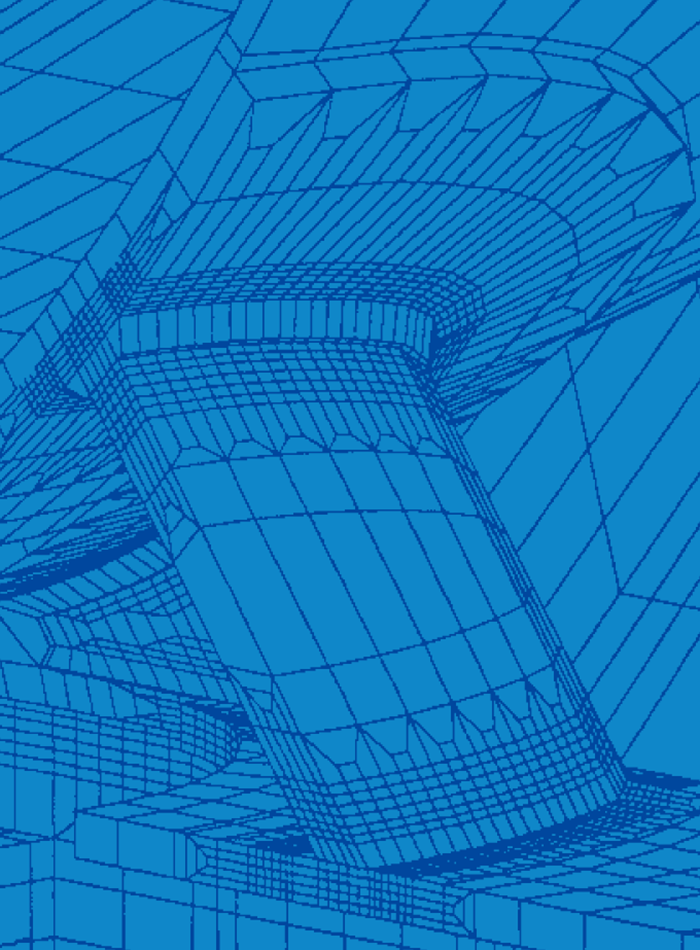
The science of damage tolerance
HLA’s diverse background gives us a unique combination of analytical and experimental capabilities that can be applied for a vast range of problems in damage tolerance.
The science of damage tolerance is multidisciplinary involving a combination of fatigue and fracture of metallic and polymeric materials, structure and component design, manufacturing quality, damage detection, monitoring systems and structural reliability. HLA’s extensive experience includes all of the above disciplines including loads, materials, computational procedures, structural analysis, stress analysis, and fatigue and fracture mechanics analysis.
Using a combination of these disciplines, HLA is capable of performing complex fatigue life predictions and fracture mechanics characterizations to evaluate the structural integrity of your commercial structures.
Our experience includes:
FEA of structures using commercial finite element programs like ANSYS, and LS-DYNA with linear and nonlinear elasticity and plasticity stress analyses.
Fracture mechanics including residual strength of cracked components, crack growth, arrest and damage tolerance.
Railroad tank and freight cars, fatigue in railroad structures, construction materials, fatigue in pressure vessels, ASME pressure vessel and boiler codes.
Fatigue in aircraft and helicopter structures, advanced composites, design of composites, polymers and elastomers, adhesives, joining and interlaminar fracture, fatigue of polymers, polymer matrix composites, matrix cracking and fiber failure.
S-N curves, endurance limits and fatigue strength evaluation, mean stress effects, Goodman & Haigh diagrams.
Fracture Toughness — Thickness and directionality effects, residual strength, creep and thermal fatigue and radiation.
Crack Initiation and Propagation, crack arrest and multiple load paths studies, Paris, Forman, & Walker equations, crack growth calculations, variable amplitude loading, retardation, Willenborg, Wheeler, and closure models, multiaxial loadings — mixed mode crack problems, progressive cracking and damage models, cracking at structural holes, loaded and unloaded structural holes, structural failure modes: creep, fatigue, and corrosion cracking etc.
Load spectrum analysis, sequence effects, truncation, clipping and retardation.
NASA FLAGRO and NASGRO crack growth computer programs.
Establishing structural inspection intervals, POD analysis, Weibull analysis for reliability.
HLA provides the level of experience you demand in design, analysis, testing and computation capabilities in DTA. We have partnered with research organizations and universities and have worked extensively in identifying practical efficient and cost effective methods of evaluating durability and damage tolerance of structures.accumulation and MINER’S rule and it’s applicability.
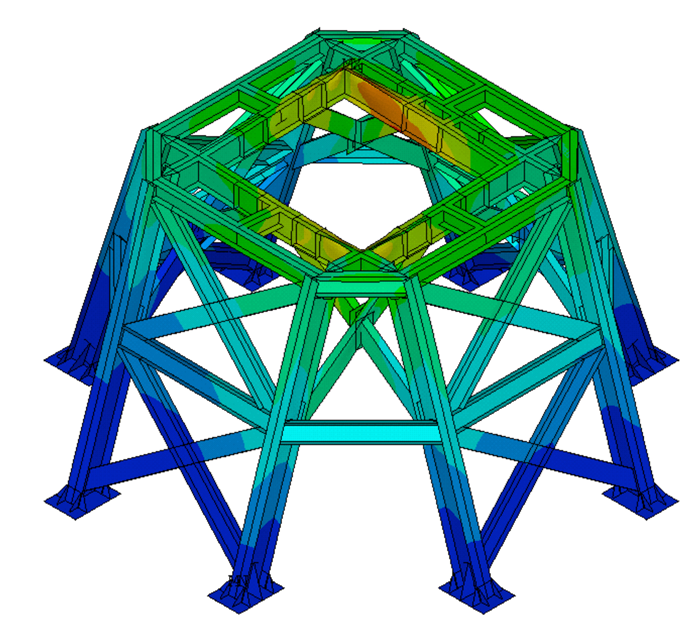
Types of stress analysis
HLA’s professional engineers can provide stress analysis to exacting requirements from classical and Finite Element Analysis (FEA) to formal reports and documentation for all materials such as aluminum, carbon, stainless steels, composites and elastomers.
Our engineers possess the combined experience necessary to provide FEA for the design of complex structures and/or manufactured products constructed of any material. We also have extensive analyses experience with stress, thermal, vibration, and fatigue. HLA can develop practical and accurate finite element models of your product or structure from engineering drawings or from electronic data files.
HLA can also provide collaborative services where our team partners with your engineering department to provide analysis support for on-going or periodic design projects. In addition, we can assist in the design process to help create optimal results that meet all your design criteria.
HLA leverages FEA programs like ANSYS and LS-DYNA. We have several in-house custom FEA programs for the analysis of metal and elastomeric parts.
Major benefits of Computer Simulated Stress Analysis
Major benefits of Computer Simulated Stress Analysis
Reducing the product weight
Increasing the product strength and stiffness
Reducing product design time
Reducing premature product failure
Optimizing manufactured product design
Reducing number of initial tests
HLA provides:
Design of structural steel, concrete, and wood frame members and connections
Design of FRP structures
Design of unique structures and unique loading criteria
Design for extreme loads such as wind and earthquake
Design for vibration isolation of structures and supported equipment
Reduction of potential for fatigue and fracture of structures and connections
90 years experience in finite element analysis
Design of structural steel, concrete, and wood frame members and connections
Material non-linearity
Large displacement-stress stiffening
Contact
Transient dynamic
Buckling/post buckling
Heat transfer
Conduction
Convection & radiation – steady state or transient
Creep/seepage
Engineering physics
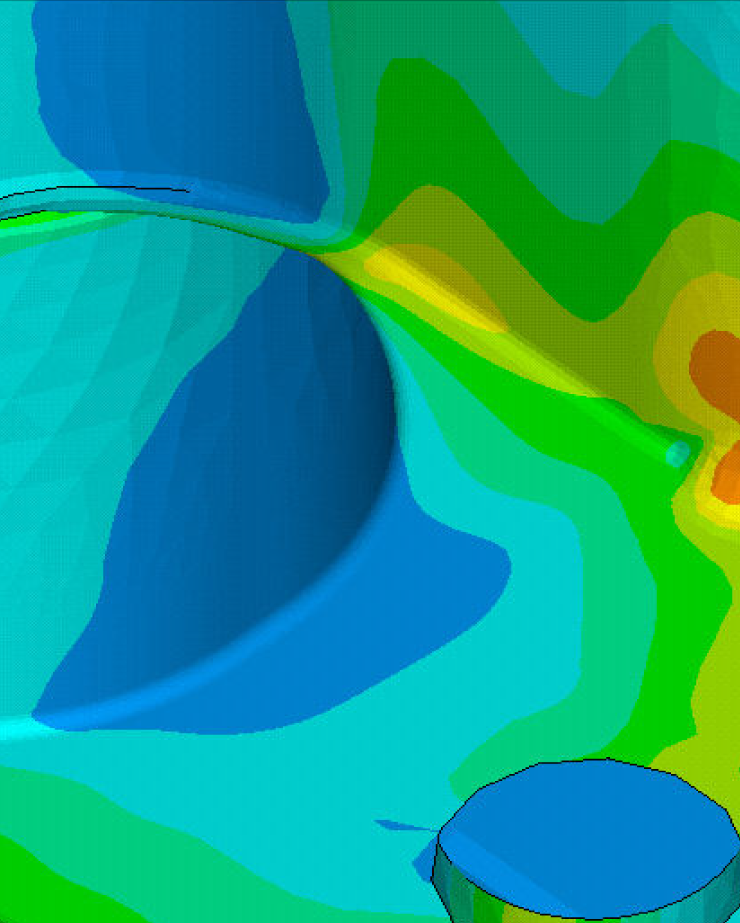
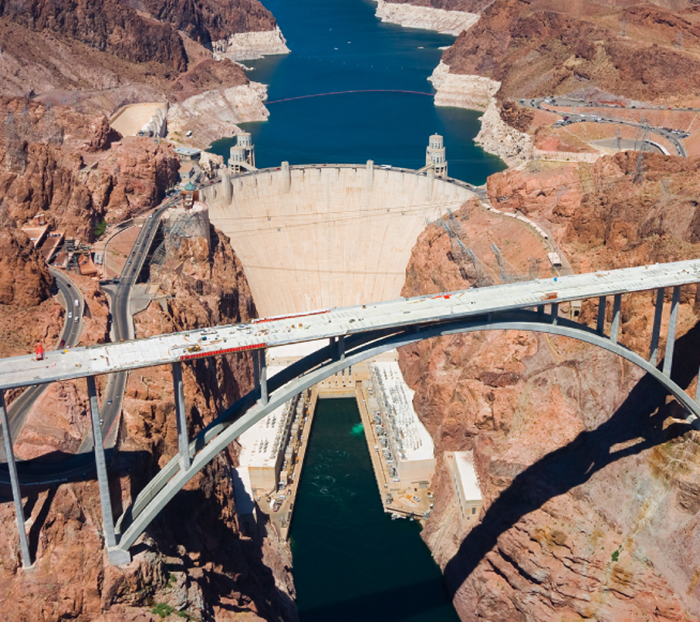
The Depths of Our Analysis
As forensic engineers, HLA provides the expertise you require in determining the causes of accidents of all kinds including industrial incidents, collapses, fires and explosions. We reconstruct these accidents and incidents to explain the events to our clients and, when necessary, to juries. We are experienced in a wide range of engineering disciplines, and we supplement our skills as required with a variety of experts from other fields including metallurgy, electrical, etc.
We go far beyond that to provide our clients with much more:
We go far beyond that to provide our clients with much more:
What happened?
Why did it happen?
How we can prevent it from happening again?
Who, if anybody, caused it to happen?
How much it will cost and how long will it take to rebuild?
Are the reported repair costs reasonable?
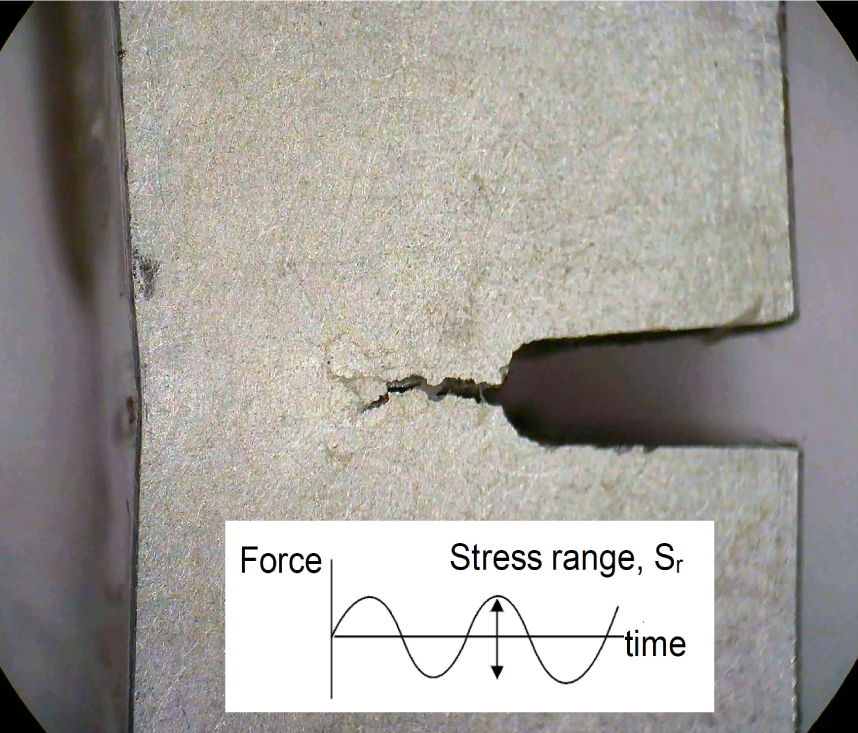
As a full service Structural / Mechanical Engineering Company, we can provide both Turn-Key and Special Project Design and Computer/Stress Analysis to companies locally, nationally and internationally: Trinity Industries, Goodyear, General Electric, L-3 Communications, Raytheon and Shell Oil, to name a few.
HLA can provide state-of-the-art design and analysis capabilities, based on CAD & Finite Element Computer Methods. HLA uses state-of-the-art software: ANSYS, LS-DYNA, STAAD, AutoCad, SolidWorks, Pro-E, combined with both HP-mainframe and Super PC-desktop hardware networked to provide the capability of solving the largest – most difficult problems.
Our consulting experience includes:
Transportation
Industrial
Power Generation
Elastomers
Rail
Intermodal
Petrochemical
Composites
Cargo
Aircraft
Offshore Engineering
Software Development